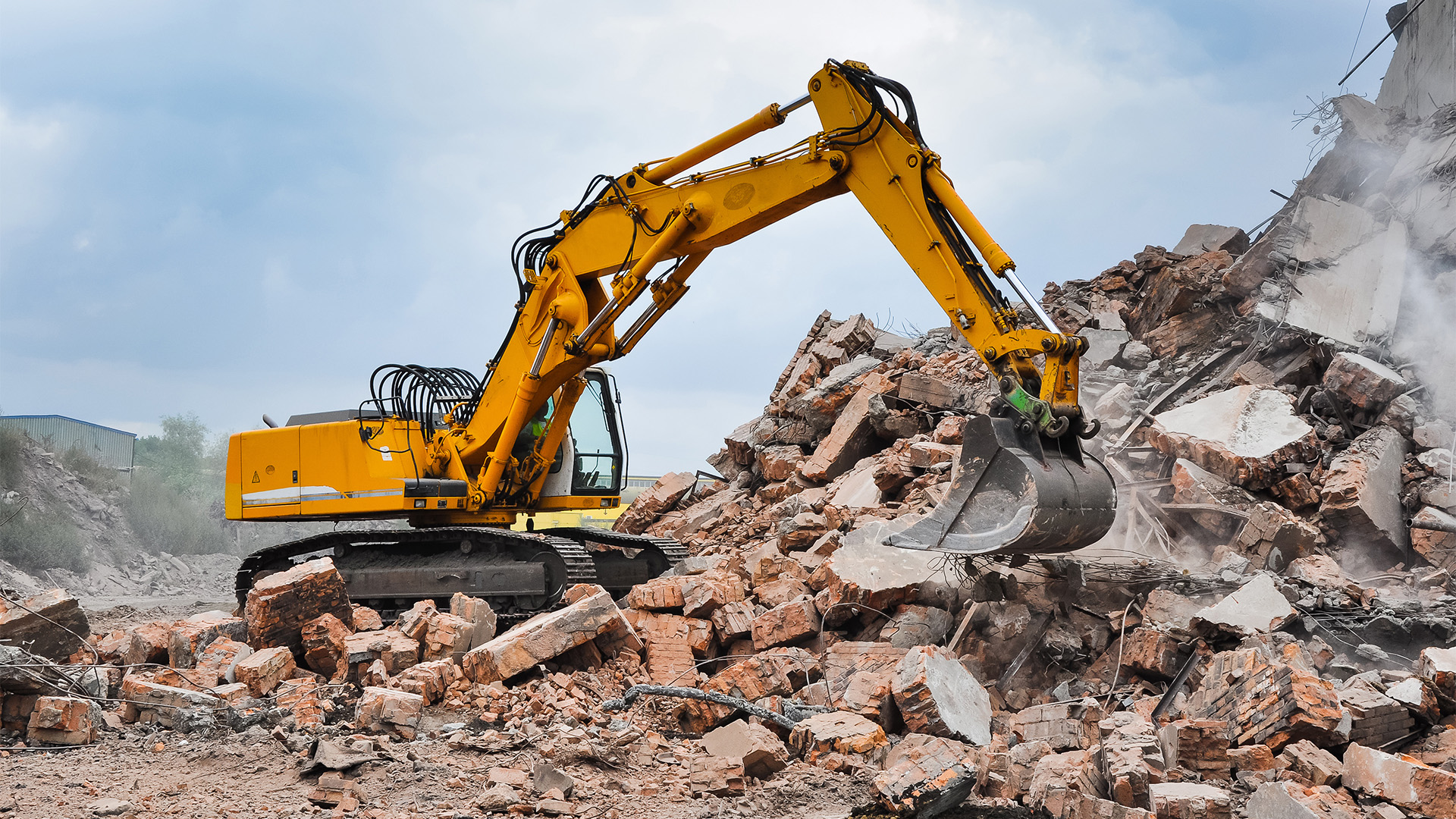
By Evelyn Long, Editor-in-Chief of Renovated
Building demolitions can be highly profitable projects for construction companies. However, they often pose many safety hazards to workers and the surrounding community. Managers overseeing demolition sites must watch out for these seven common dangers to protect their employees and the environment.
1. Falls From Heights
Falling from tall buildings or equipment is the greatest threat to worker safety during demolition projects. Accidents related to slips, trips and falls caused 850 workplace fatalities in the United States in 2021, primarily on construction sites. Falling injuries are also the leading cause of missed workdays and workers’ compensation claims.
Demolition site managers can address this hazard in several ways. They should ensure employees have proper safety equipment, training and licensing for operating heavy machinery. They must also take great care when inspecting the equipment involved in the project.
The Occupational Safety and Health Administration (OSHA) outlines strict rules for employees working 6 feet above ground level or higher. These rules mainly focus on using safety monitoring devices and fall prevention equipment. Some conventional gear OSHA mentions are guardrails, safety nets and personal fall arrest systems.
2. Falling Debris
Once demolition begins, falling debris will become an immediate danger to everyone around the building. Site managers can’t control how things fall but can determine where the pieces land using commercial debris netting. The tightly woven polyethylene nets catch bricks, chunks of concrete and other loose items that fall near employees.
Personal protective equipment is also essential for protecting workers from falling objects. Everyone on the site should always wear hard hats and safety glasses, regardless of their specific roles. Putting cautionary signage around the worksite is another basic safety measure to keep employees alert.
3. Hazardous Materials
Demolition projects usually involve older buildings full of hazardous materials, including asbestos, lead, polychlorinated biphenyls (PCBs), chlorofluorocarbons (CFCs) and numerous heavy metals. Workers can make close contact with these materials and potentially develop short- and long-term health problems.
For example, a study of old houses in Vermont found that 75% of bathtubs had lead in the enamel glaze. Seemingly harmless objects can include toxic ingredients, so site managers must provide respiratory protection and ventilate the site. A thorough predemolition inspection will also help workers steer clear of contaminated items.
4. Toxic Fumes
Managers should also account for airborne pollutants. Demolitions account for 90% of all construction waste, most of which consists of smoke, dust, volatile organic compounds (VOCs) and other toxic fumes. This waste negatively affects employee health, local air quality and nearby waterways.
The best way to mitigate this threat is by providing workers with respiratory equipment and maintaining proper ventilation in enclosed areas. Daily air quality monitoring is also essential for preventing inhalation and avoiding health emergencies.
5. Electric Shock
Electrocution is a constant threat during demolitions because exposed live wires are everywhere. The first step to addressing this problem is deenergizing electrical equipment before working on it. Workers simply must shut down old machinery and unplug everything before demolition begins.
Another simple yet effective safety precaution is hiring an electrician subcontractor to deal with live wires and help other workers identify dangerous electrical utilities. The most hazardous areas are places with water or damp substances because they are natural conductors of electricity.
6. Fires and Explosions
Fires and explosions can occur during a demolition project if the building includes flammable materials — namely wood, sheetrock and gypsum boards. Additionally, many chemicals used in construction could start a fire if workers mishandle them. Gasoline, fuel, linseed oil and kerosene are just a few examples.
Employee awareness is the key to avoiding fire-related accidents. Managers must inform the workforce about the presence of all flammable substances on-site. They should also store flammable liquids in their proper containers labeled with cautionary signage. There should be a strict no-smoking policy near the demolition site.
7. Noise Pollution
Demolition projects are notorious for causing lots of noise pollution, which can affect entire neighborhoods. Loud noises don’t pose a lethal threat to employees, but they can cause hearing loss. About 14% of construction workers report having hearing difficulties, and 25% have a hearing impairment that affects their day-to-day activities.
All personnel near the demolition site must wear hearing protection, especially those operating heavy machinery. Protective equipment helps employees avoid hearing troubles and make their work environments less stressful. Loud noises take a toll on the mind as well as the body, and managers should ensure workers can block out irritants and focus on their tasks.
Safety Leads to Success
Demolitions are straightforward on the surface. A construction company takes a bunch of heavy equipment and knocks the building down piece by piece. However, the finer details reveal many health and safety hazards that can affect workers and others nearby. Addressing these issues will lead to a much safer project for everyone involved and ensure everything runs smoothly.