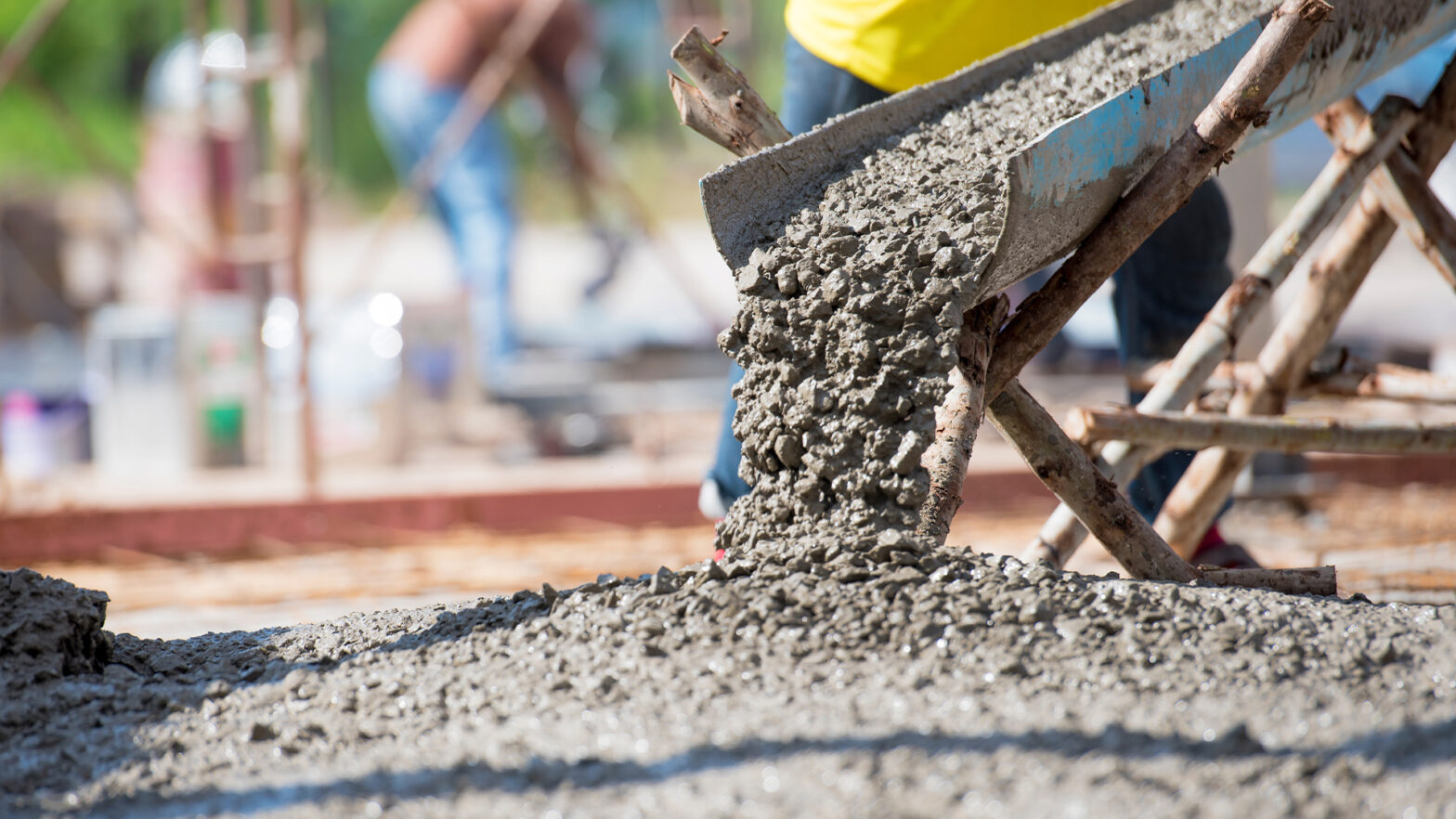
Cement, the foundation upon which our modern infrastructure is constructed, both literally and figuratively, stands as a contradictory pillar of our built environment. While indispensable for erecting skyscrapers, bridges, and roads, the global cement industry casts a long environmental shadow. Producing cement is an energy-intensive process that generates substantial carbon dioxide emissions, accounting for a staggering 8% of global CO2 output. This figure eclipses the carbon footprints of industries often perceived as more polluting, such as aviation and aerospace, underscoring the cement sector’s significant contribution to climate change.
In response to growing societal and regulatory concerns, governments and industry stakeholders are implementing a range of incentives and regulations to drive efficiency and reduce the environmental impact of cement production. Welding Alloys, a leading expert in cladding and hardfacing applications, delves into the evolving landscape to explore innovative solutions that can enhance cement manufacturing processes and contribute to a more sustainable future.
Zero Carbon Cement
Recognising the urgent need to mitigate climate change, the cement industry has committed to a decarbonisation pathway. Leading manufacturers have developed ambitious plans to reduce carbon dioxide emissions by 30% per tonne of cement produced by 2030, setting their sights on a net-zero target by 2050. This industry-wide drive towards sustainability is crucial for achieving a low-carbon future.
A key incentive for the cement industry’s decarbonisation efforts is the European Green Deal. This ambitious EU initiative aims to transform the continent into a sustainable and thriving region by eliminating reliance on fossil fuels and finite resources. The Green Deal serves as a blueprint for the cement industry’s transition to a low-carbon future.
How CBAM Will Reshape Global Trade
The EU has established strict sustainability standards for cement production, driving a push for environmentally responsible practices. To ensure a level playing field for European cement manufacturers and prevent carbon leakage, the Carbon Border Adjustment Mechanism (CBAM) was introduced. Approved in April 2023 and set for implementation in 2026, the CBAM imposes a carbon price on imports of cement and cement-related products from countries with less stringent climate regulations, reducing global decarbonisation efforts.
By implementing CBAM, it represents a pivotal step in the European Union’s efforts to establish equality for cement producers while promoting environmental sustainability. CBAM imposes a carbon price on imported cement, this ensures that products entering the EU market adhere to comparable environmental standards as those manufactured domestically. This mechanism serves to mitigate the risk of carbon leakage, a phenomenon, which production shifts to regions with less stringent environmental regulations. It is imperative to recognise that the quality of cement is intrinsically linked to its long-term performance and durability. Inferior cement is naturally more liable to the detrimental effects of wear and abrasion, making it a necessary to introduce additional protective measures such as industrial hardfacing to safeguard against premature degradation.
The operational efficiency and environmental performance of cement plants are significantly influenced by the condition of their basic parts. The deterioration of components due to wear and abrasion is a critical factor contributing to increased energy consumption within the cement production process. This heightened energy demand subsequently leads to a corresponding rise in carbon dioxide emissions. Implementing robust maintenance and repair strategies, such as industrial hardfacing, is essential in mitigating these issues. By restoring worn components to their original condition, these practices not only extend equipment lifespan but also optimise energy efficiency. This, as a result, reduces carbon emissions, making a tangible contribution to the overall environmental sustainability of the cement industry.
Furthermore, the manufacturing of new components for cement plants is a resource-intensive process that incurs a substantial energy expenditure. This energy consumption is a significant contributor to carbon dioxide emissions released into the atmosphere. Thus, prioritising the maintenance and repair of existing components over outright replacement emerges as a compelling strategy for both economic and environmental sustainability. By extending the lifespan of components through repair, the cement industry can mitigate the energy-intensive production of new parts, thereby reducing its carbon footprint and optimising resource utilisation.
Building a Circular Cement Industry
The growing emphasis on sustainability across various industries has ignited a global movement towards waste reduction, resource optimisation, and the promotion of circular economy principles. The cement industry stands at a pivotal juncture in this transformative landscape. The Circular Economy Action Plan, a strategic framework designed to minimise waste and maximise resource efficiency, has profound implications for sectors deeply intertwined with cement, such as construction and building. By prioritising recycling, reuse, and the development of innovative waste management solutions, the cement industry can significantly contribute to a more sustainable and resilient future.
A foundation of the plan is to encourage the exploration of alternative raw materials and energy sources for cement production, with the aim of reducing the industry’s environmental footprint. This involves a strategic shift towards utilising recycled materials, such as aggregates recovered from construction and demolition waste, as well as investigating the potential of biomass as a fuel source. By embracing these innovative approaches, the cement industry can decrease its dependency on virgin resources and reduce its carbon emissions, contributing to a more sustainable future.
Sustainable Cement Solutions
The development of carbon-neutral cement production processes is a critical component in the cement industry’s efforts to align with the ambitious sustainability targets established by European governments. While the challenges associated with achieving carbon neutrality are substantial, recent advancements suggest that the production of sustainable cement may be within closer reach than previously anticipated.
A collaborative endeavour spanning two years, the Cement 2 Zero (C2Z) project was directed by the Materials Processing Institute and the University of Cambridge, with generous financial backing from UK Research and Innovation (UKRI). This ambitious initiative brought together a group of industry leaders, including engineering and design powerhouses Atkins and Balfour Beatty, as well as key supply chain partners such as Tarmac, CELSA, and Days Aggregates. This unique partnership aimed to harness collective expertise and resources to develop innovative solutions for the decarbonisation of the cement industry.
The Cement 2 Zero (C2Z) project is currently undergoing a trial testing phase to evaluate its performance under real-world construction conditions. After successful completion of these comprehensive assessments, the innovative cement will be implemented on an active UK construction site, marking a crucial milestone in the project’s development. If the carbon emissions generated during large-scale production align with the promising results achieved in the laboratory, it could significantly accelerate the cement industry’s progress towards carbon neutrality. This potential breakthrough could redefine cement manufacturing processes, making them substantially more efficient and environmentally friendly.
One thing that’s clear is that substantial government support for research and development is vital for propelling the cement industry towards its ambitious sustainability goals. The industry’s capacity to innovate and implement groundbreaking solutions will be significantly enhanced through strategic investments in research and development. Similar to the government’s proactive stance on the automotive sector, with the impending ban on the sale of new petrol and diesel cars by 2030, targeted support for the cement industry can accelerate the adoption of sustainable practices. By fostering a collaborative environment between industry and government, the potential for developing and commercialising low-carbon cement technologies can be maximised, ultimately contributing to a more sustainable future.