Hiring heavy equipment is costly and time consuming whether you are a construction company or an individual project. There is a process to be observed, and after securing the contract, it is essential that you get the most out of the equipment during the time it is with you. This post focuses on what you need to know about optimising your time with any heavy equipment hire so that you don’t lose out on essential outputs.
What You Need
If you’re not sure which heavy machinery option is best suited to your particular project, it is better to enquire with the experts to avoid spending money on an incorrect asset. To keep a construction zone running smoothly, the machinery you hire in has to fit the brief. Figure out what you need in exceptionally clear terms and use this as a sounding board for negotiations when you have shortlisted a few options to peruse.
Prepare the Turf
Regardless of which stage you bring in the heavy equipment, the project site has to be ready for it. There is little to no sense in bringing in the machinery just for it to sit dormant, therefore wasting time and money, while you then prep the site for use. So, well in advance of securing the contract, plan your space and get it ready for the machinery stage. This includes:
- Informing any workers about what’s to come and helping them prepare
- Clearing the area of anything that would impede task completion objectives
- Acquiring the basics like PPE and zoning props
- Completing any mandatory training well before the hiring day
Trust the Experts, Avoid the Scams
When searching for digger hire, or similar, the source company has to be reputable. If it turns out to be less than credible, for instance, not only is your whole project at risk but your health and safety will be too. Companies like Boels understand what you need, the most direct way to get the job done, and provide trustworthy equipment that you can rely on. Heavy machinery needs:
- Regular maintenance schedules to check all the parts are doing as they should be
- Frequent cleaning to remove debris and ensure a high-quality output
- Parts inspections after a period of use
- A person from the company on standby with any safety advice if necessary
- There are lots of scam companies that exist to take your money while providing you with dodgy equipment that puts your life at risk and project too.
- Be wary and steer clear of any corporation that has outdated material with little or no proof of maintenance history.
Furthermore, anywhere where there is no provided contract or stipulated safety protocol to follow.
Work within a Limit
Everything on earth has a limit, and heavy equipment machinery is not exempt from this. Though you might be tempted to push boundaries, it is advisable to avoid this at every stage. Why? Simply because, if you ask too much of the machine it will most likely malfunction and put everything in peril. You risk becoming injured or hurting someone close by and you open the door for the machinery becoming broken and therefore uprooting the whole project. Despite the desire to get things done quickly and as efficiently as possible, in this context, patience really is a virtue. Understand the limits and stick to the boundaries so you don’t risk everything and leave yourself liable for repair costs, hiring penalties, compensation claims or hospital stays.
Verify the Maintenance and Upgrade History
Always ask to see maintenance logs because it proves the machinery is up to date and safe. Safety is a clear concern when carrying out construction projects in any setting. Proper maintenance is the responsibility of the owner, and whoever is hiring it too. Though the more substantial jobs such as part replacement and upgrade modifications are always in the remit of the owner, other things like cleaning and observations should be carried out by the person currently using the machinery. These are tasks such as basic cleaning, dusting and debris removal to remove any danger of blockage and seizure.
Consider an Operator
Without comprehensive training, lots of equipment is inaccessible. Thankfully, there are options if you don’t want to spend time completing training hours and tasks. The easiest route is to find room in the budget for an equipment operator. Most reputable hiring firms will have a bunch of associated contractors that they also hire out to operate machinery. By taking this route, not only do you guarantee that everything will be done properly by a highly trained professional, but you save time as well and minimise potential mistakes being created by a novice user. It is also usually more convenient in general, as most firms that offer this option will provide operator and machine as a package deal that is taken away at the end of each day, therefore eliminating the need for you, the renter, to provide secure storage while not in use.
Ultimately, what you hire will depend on the task that needs doing. Regardless, it is something that demands time, money and space so it needs careful consideration in any context. This is not a decision to dive in headfirst without thinking it through. To really optimise your hire period, make sure every aspect you can prepare for, is prepared. Do the training, obtain the safety gear and keep the team up to date with any developments.
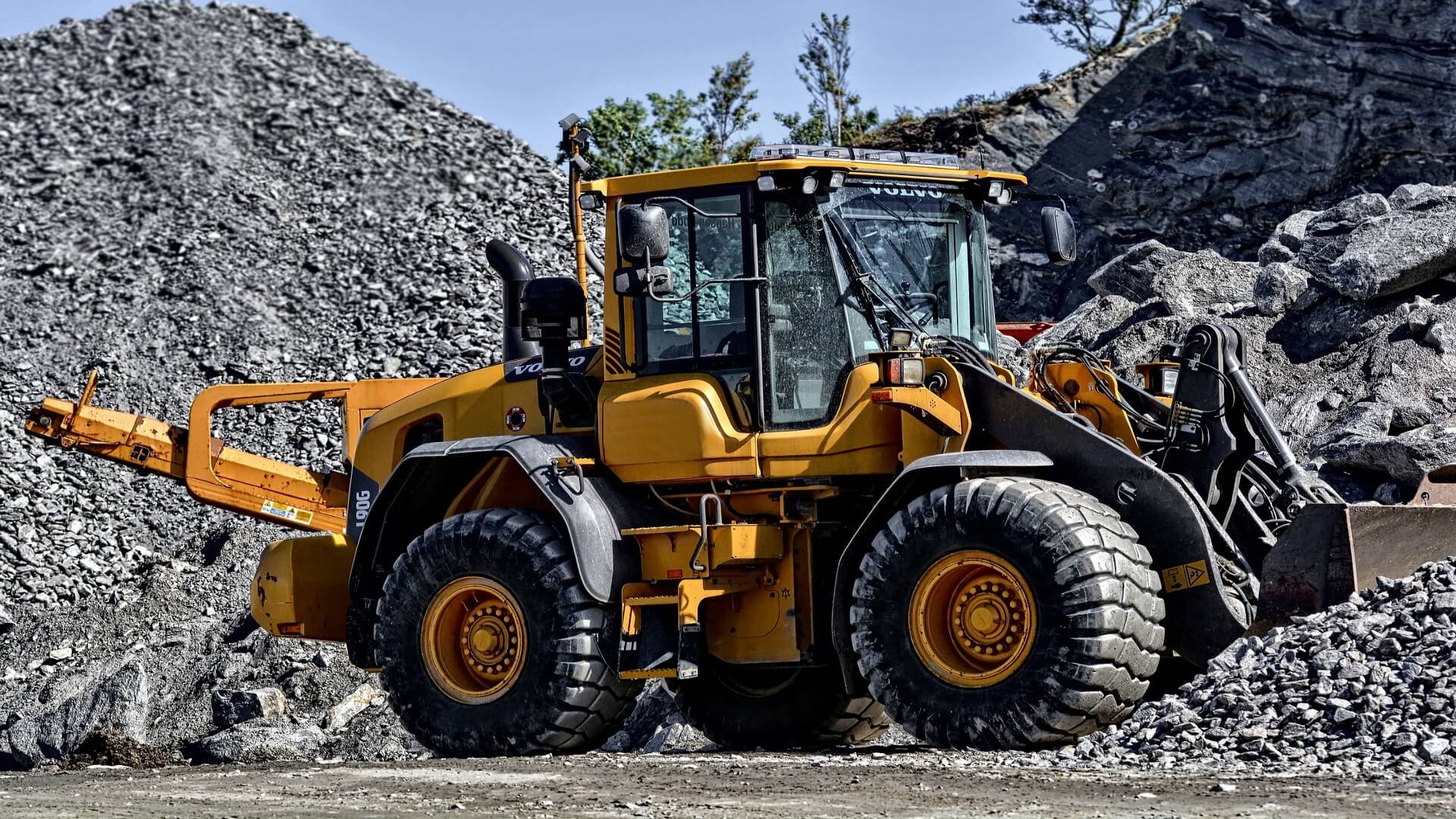